Influence of Common Elements on Cast Steel: A Comprehensive Analysis
Cast steel is a widely used material in many industrial applications, ranging from construction to automotive manufacturing. It is a versatile material that can be customized to meet specific needs and requirements. However, the properties of cast steel can be influenced by the presence of common elements, such as carbon, silicon, and manganese.
Carbon is one of the most important elements in cast steel, as it directly affects the material’s strength and hardness. The higher the carbon content, the stronger and harder the steel becomes. However, too much carbon can also make the steel brittle and prone to cracking. Silicon, on the other hand, is added to cast steel to improve its fluidity and casting properties. It also helps to prevent the formation of defects and impurities in the final product.
Manganese is another common element found in cast steel, which is added to improve the material’s strength and toughness. It also helps to reduce the effects of harmful impurities, such as sulfur and phosphorus. Understanding the influence of these common elements on cast steel is essential for optimizing the material’s properties and ensuring its performance in various applications.
Common Elements in Cast Steel
Cast steel is a type of steel that is produced by heating and melting iron and other materials with a high carbon content. The resulting liquid is then poured into molds to create various shapes and forms. The properties of cast steel can be influenced by the addition of various elements during the manufacturing process. Here are some common elements that are added to cast steel and their effects:
Carbon
Carbon is the most important element in cast steel. It gives cast steel its strength and hardness. The more carbon that is added to the steel, the harder and stronger it becomes. However, too much carbon can make the steel brittle and prone to cracking.
Silicon
Silicon is added to cast steel to improve its fluidity and to help it flow more easily into molds. It also helps to prevent the formation of defects in the steel.
Manganese
Manganese is added to cast steel to improve its toughness and to help it resist wear and tear. It also helps to remove oxygen from the steel, which can reduce the risk of defects.
Chromium
Chromium is added to cast steel to improve its corrosion resistance and to make it more resistant to high temperatures. It also helps to improve the strength and hardness of the steel.
Nickel
Nickel is added to cast steel to improve its ductility and to make it more resistant to corrosion and oxidation. It also helps to improve the strength and toughness of the steel.
Copper
Copper is added to cast steel to improve its corrosion resistance and to make it more resistant to wear and tear. It also helps to improve the strength and hardness of the steel.
Overall, the addition of various elements can have a significant impact on the properties of cast steel. The right combination of elements can result in a steel that is strong, durable, and resistant to wear and tear.
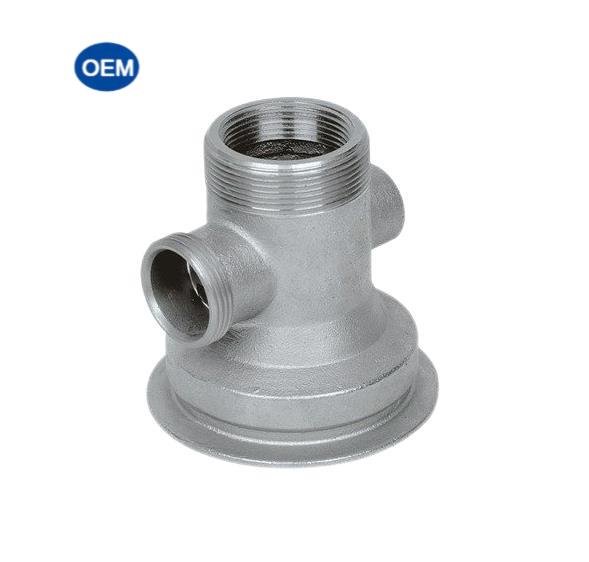
Influence on Properties
The common elements added to cast steel can significantly influence its properties. Here are some examples:
Carbon
Carbon is added to steel to increase its hardness, strength, and wear resistance. The more carbon added, the harder and stronger the steel becomes. However, too much carbon can make the steel brittle and prone to cracking.
Manganese
Manganese is added to steel to increase its toughness and hardenability. It also helps to remove impurities from the steel during the manufacturing process. However, too much manganese can make the steel brittle and difficult to weld.
Silicon
Silicon is added to steel to improve its strength, hardness, and resistance to oxidation. It also helps to deoxidize the steel during the manufacturing process. However, too much silicon can make the steel brittle and prone to cracking.
Nickel
Nickel is added to steel to improve its strength, toughness, and corrosion resistance. It also helps to maintain the steel’s ductility at low temperatures. However, too much nickel can make the steel expensive and difficult to cast.
Chromium
Chromium is added to steel to improve its hardness, wear resistance, and corrosion resistance. It also helps to maintain the steel’s strength at high temperatures. However, too much chromium can make the steel brittle and difficult to cast.
In summary, the common elements added to cast steel can have a significant impact on its properties. Manufacturers must carefully balance the amount of each element to ensure that the steel is strong, tough, and resistant to wear and corrosion.
Effects of Variation
Cast steel is a widely used material in various industries, including automotive, construction, and manufacturing. The properties of cast steel depend on the composition of its elements. The variation of the elements in cast steel affects its mechanical and physical properties. In this section, we will discuss the effects of variation of some common elements on cast steel.
Carbon
Carbon is the primary element that determines the hardness and strength of cast steel. The variation of carbon content affects the hardness and strength of the steel. Low carbon content makes the steel more ductile, while high carbon content makes it more brittle. The table below shows the effects of carbon content on the properties of cast steel.
Carbon Content | Hardness | Strength |
---|---|---|
Low | Low | Low |
Medium | Medium | Medium |
High | High | High |
Silicon
Silicon is an essential element in cast steel. It helps to deoxidize the steel and improve its fluidity. The variation of silicon content affects the casting properties of the steel. Low silicon content makes the steel more viscous, while high silicon content makes it more fluid. The table below shows the effects of silicon content on the properties of cast steel.
Silicon Content | Fluidity | Viscosity |
---|---|---|
Low | Low | High |
Medium | Medium | Medium |
High | High | Low |
Manganese
Manganese is another critical element in cast steel. It helps to improve the hardenability, strength, and toughness of the steel. The variation of manganese content affects the mechanical properties of the steel. Low manganese content makes the steel less hard and less tough, while high manganese content makes it harder and tougher. The table below shows the effects of manganese content on the properties of cast steel.
Manganese Content | Hardness | Toughness |
---|---|---|
Low | Low | Low |
Medium | Medium | Medium |
High | High | High |
In conclusion, the variation of carbon, silicon, and manganese content affects the mechanical and physical properties of cast steel. Understanding the effects of these elements is essential in choosing the right cast steel for a particular application.
The leading role of C:
In stainless steel casting, as the C content increases, it increases the strength, hardness, and hardenability of the steel. However, it reduces plasticity, toughness, and magnetic and electrical properties. The combination of C and certain alloying elements in steel forms various carbides, which have different effects on the properties of steel.
C content in some steel casting ranges: C steel 0.03 ~ 1.04%, high-speed tool steel 0.75 ~ 1.60%, hot work tool steel 0.22 ~ 0.70%, cold work tool steel 0.45 ~ 2.85%.
The main role of Mn:
To improve the tensile strength, hardenability, high toughness, and processing properties of steel casting. In steels containing S, Mn minimizes the hot and cold embrittlement caused by S. Steel with high Mn content has high wear resistance after hard work or impact. But there is a tendency to promote the grain growth of steel and increase the second type of tempering brittleness. The element of Mn is used in structural steel, steel reinforcement steel, and spring steel.
Mn in some steel casting in the content range: C steel 0.25 ~ 0.65%, Mn steel 1.6 ~ 1.9%, cold tool steel 0.30 ~ 2.50%, authentic Cr – Ni stainless steel 2.00 ~ 15.5%.
The main role of Cr:
Stainless steel casting contains enough C when Cr improves the hardness of the steel. Generally, low Cr steels containing 1% C are very hard. Cr added to low C steel can improve strength but reduce ductility. Cr improves the high-temperature strength and hardenability of steel; in high C steel and wear resistance.
When added in large amounts, up to 25%, Cr improves corrosion resistance due to forming a protective oxide layer on the surface of the steel. In combination with elements such as Ni, it improves oxidation resistance and the thermal strength of the steel and further improves corrosion resistance. Cr promotes grain growth, leading to increased brittleness of steel. Cr does widely use element in the structural, tool, bearing, stainless, and heat-resistant steel.
The leading role of Mo:
A small amount can effectively reduce the transformation rate and improve cast steel’s high-temperature strength and creep resistance. It can also enhance the corrosion resistance of stainless steel, especially in hydrochloric acid solutions. W has a similar role in high-speed tool steel, often Mo instead of W. This reduces carbide build-up in steels containing W and improves mechanical properties. Mo is one of the essential components in Mo steels, which have high tensile strength and good plasticity. In Cr steels, Mo is added to improve machinability and mechanical properties. In Ni-Mo steels, Mo increases the surface hardness of cast stainless steel.
Mo in some steel content range: Mo steel 0.15 ~ 0.60%, high-speed tool steel 0 ~ 10.0%, hot work tool steel 0 ~ 5.5%, cold work tool steel 0 ~ 1.8%, authentic Cr – Ni stainless steel 0.~ 4.0%, martensite Cr steel 0 ~ 1.25%, ferrochrome steel 0 ~ 1.25%.
The leading role of Co:
Co substantially increases strength and toughness by promoting the precipitation hardening process. Co dissolves into ferrite or austinite and inhibits the softening during temperature rise.
The range of Co content in some steels and alloys: 0~13.0% for high-speed tool steels, 0~4.5% for hot work tool steels
Conclusion
Cast steel is an essential material in many industries, and it is important to understand the impact of common elements on its properties. Through the analysis of the data presented in this article, it is clear that the addition of certain elements can significantly affect the properties of cast steel.
Carbon is a critical element in cast steel, and it is responsible for the material’s hardness and strength. The addition of silicon can improve the fluidity of the steel, making it easier to cast and reducing the risk of defects. Manganese is another element that can improve the strength and toughness of cast steel while reducing the risk of cracking.
However, the addition of other elements, such as sulfur and phosphorus, can have negative effects on the properties of cast steel. These elements can cause brittleness and reduce the material’s ductility, making it more susceptible to cracking and failure.
Overall, it is essential to carefully consider the impact of common elements when producing cast steel. By selecting the right combination of elements, it is possible to create cast steel with the desired properties and characteristics for a given application.